Piping & Vessel Design & Analysis | AUTOPIPE | AUTOPIPE VESSEL
Piping and Vessel Design and Analysis Software
Reduce the cost and time to produce compliant piping and vessel designs for any plant environment, including nuclear. Save time and reduce errors by importing piping models from common plant design applications to perform advanced pipe stress analysis. Deliver faster, safer, more cost effective vessel designs with automatic workflows that include complete global codes and applied loadings. Accelerate the delivery of compliant nuclear piping designs with comprehensive, nuclear-specific analysis and design code coverage.
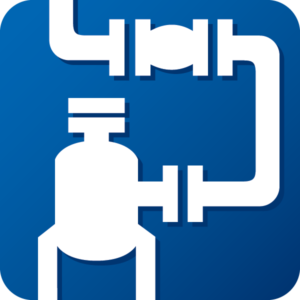
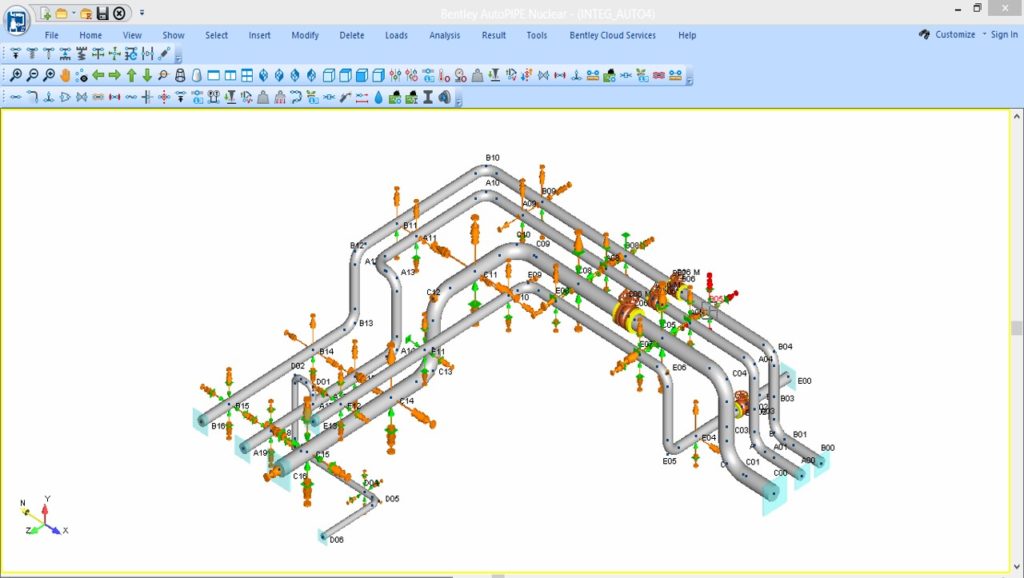
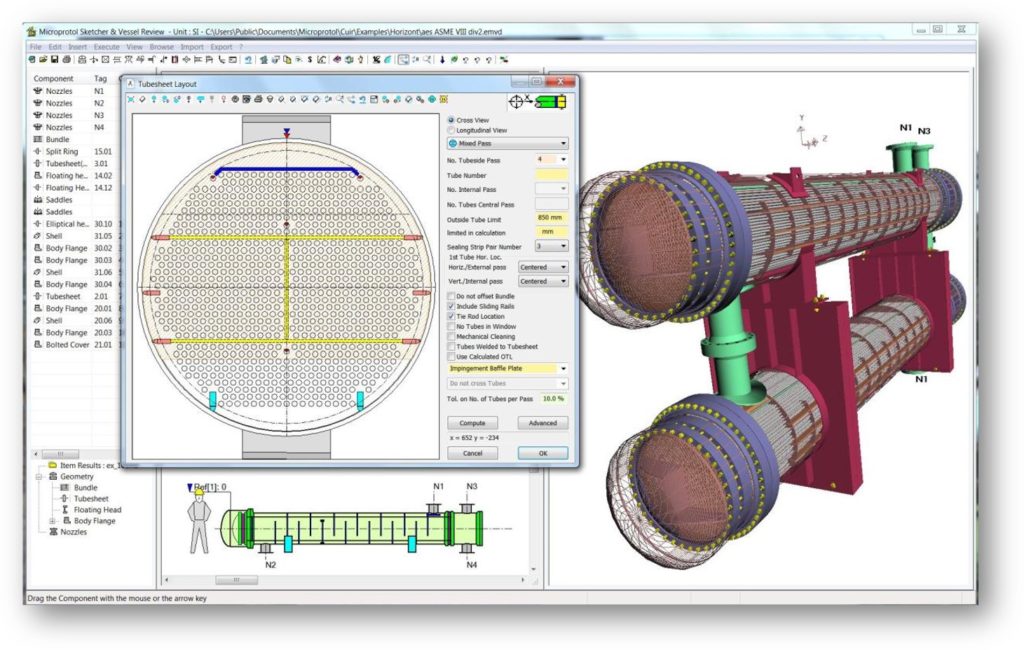
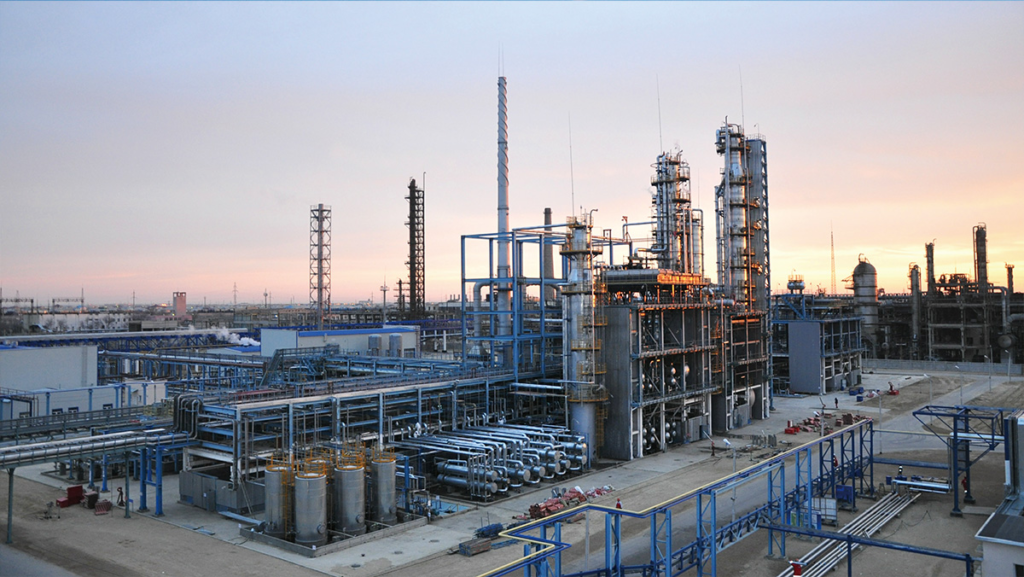
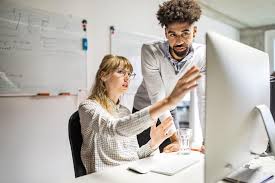
AUTOPIPE TECHNICAL OVERVIEW:
Analyze and visualize pipe stress
- Provide confidence in the safety of your engineering designs with static and load sequencing nonlinear analysis. Perform analyses to examine different loading scenarios including thermal, seismic, wind, and dynamic load cases. Instantly view stresses, deflections, forces, and moments. Save time and reduce errors with robust integration to all major intelligent 3D CAD systems.
Check pipe stress displacements and clashes
- Increase plant model accuracy by determining pipe stress displacements due to loading cases such as temperature, seismic, or other extreme loading conditions. Analyze any loading condition applied to piping and structures then use MicroStation or OpenPlant Modeler to evaluate and resolve clashes.
Comply with industry codes and standards
- Ensure your projects comply with more than 30 global design standards across the power, nuclear, offshore, chemical, and oil and gas industries. Incorporate ASME, British, European, French, Japanese, Russian, API, NEMA, ANSI, ASCE, AISC, UBC, ISO, and WRC guidelines and design limits.
Design and model piping
- Design, model, and analyze 3D piping systems to international piping specifications based on parametric component catalogs. Integrate the 3D piping model with pipe stress analysis tools to increase design quality and design productivity. Improve the overall engineering integrity and quality of piping models.
Reference structural model for pipe stress analysis
- Reuse design data by creating a structural model in STAAD or SACS and import it into AutoPIPE for a more realistic, fully integrated, bi-directional piping and structural analysis. You can also import the final piping model, complete with pipe support loads, into the Bentley STAAD or SACS model.
Leverage Bentley’s iTwin Services
- AutoPIPE is integrated with Bentley’s iTwin Services. It enables you to do more with the models you build. Each engineering analysis model that you develop can be used for collaboration, review, and exchange during the entire course of the project and beyond. Plus, the significantly value grows over time.
- AUTOPIPE VESSEL TECHNICAL OVERVIEW:
Comply with industry codes and standards
- Ensure your projects comply with more than 30 global design standards across the power, nuclear, offshore, chemical, and oil and gas industries. Incorporate ASME, British, European, French, Japanese, Russian, API, NEMA, ANSI, ASCE, AISC, UBC, ISO, and WRC guidelines and design limits.
Design and model pressure vessels
- Quickly design and model pressure vessels based on international design codes and local load methods. Optimize your flange design to minimize costs based on design codes, ensuring safe vessel design. Generate bills of material, detailed vessel drawings, and detailed parametric 3D solid models.
Generate vessel detail drawings
- Reduce manual drawing time and rework with automated detailed drawings. Create fully dimensioned engineering drawings, managing white space and configuring drawing sheet layout. Customize data and connection details to meet manufacturer standards.
Reference piping model for vessel analysis
- Save time and reduce errors by importing nozzle loads from AutoPIPE into AutoPIPE Vessel for analysis as a local load on the vessel shell.